It’s been a few weeks since I updated what we have been up to. It feels like a lifetime, but looking back from here, I wonder sometimes what all the fuss was about! Harvest finished on 19th September, which was just over 7 weeks from when we started, which is about bang on average. The last couple of weeks were a bit fraught though.
Breakdowns
I’ve mentioned in earlier posts that I was nursing the combine through harvest as best I could. We’d just had a fan bearing go, and the hydraulic oil cooler was leaking, but I was keeping an eye on things. The fan bearing and associated shafts, cogs, etc were all successfully replaced, and I got back to harvesting almost exactly a week after breaking down. I was cutting perhaps the steepest field on the farm, so was taking my time, and just about had it finished. While turning on the side of a hill, the hydraulic oil warning light/buzzer came on, but just briefly. I didn’t have much to do until I’d finished the bit I was on, so carried on until I’d emptied into the trailer at the side of the field. I’d been having to top up the hydraulic oil level periodically because of the leak, so I thought that was all I would have to do. However when I got to the back ladder, there were spots of hydraulic oil on it, which got more as I went up to the engine compartment. The cooler leak had got worse, so I limped my way down to a level part of the field next the gate, and gave Stuart at Sellars a phone again. 5 minutes later the rain came on anyway, so I didn’t lose out on much.
We lost a day and a half until the cooler was repaired, during which it rained. I managed to finish the field on the Friday, but what a change in ground conditions. Things had been damp on the Wednesday, but now they were wet. Getting up the hill was a real challenge.
The other major breakdown we had was at the grain dryer. Our dryer is a continuous flow dryer, which means that it is a column, where wet grain goes in at the top, and by the time it gets to the bottom it is dry. Grain is moved in to and away from the dryer by a system of elevators and conveyors – the elevator moving the grain up, and the conveyors in a horizontal direction. The elevator works by having a series of buckets fixed to a rubber belt, the grain being transported up in a bucket, and then chucked out at the top. Our elevator is a double legged elevator which is quite old. It has been on the radar for being replaced for a number of years, but due to costs, and restrictions of the building the dryer is in, we’ve not done anything. Our hand will be forced over the winter. The belt in the leg that handles the wet grain snapped.
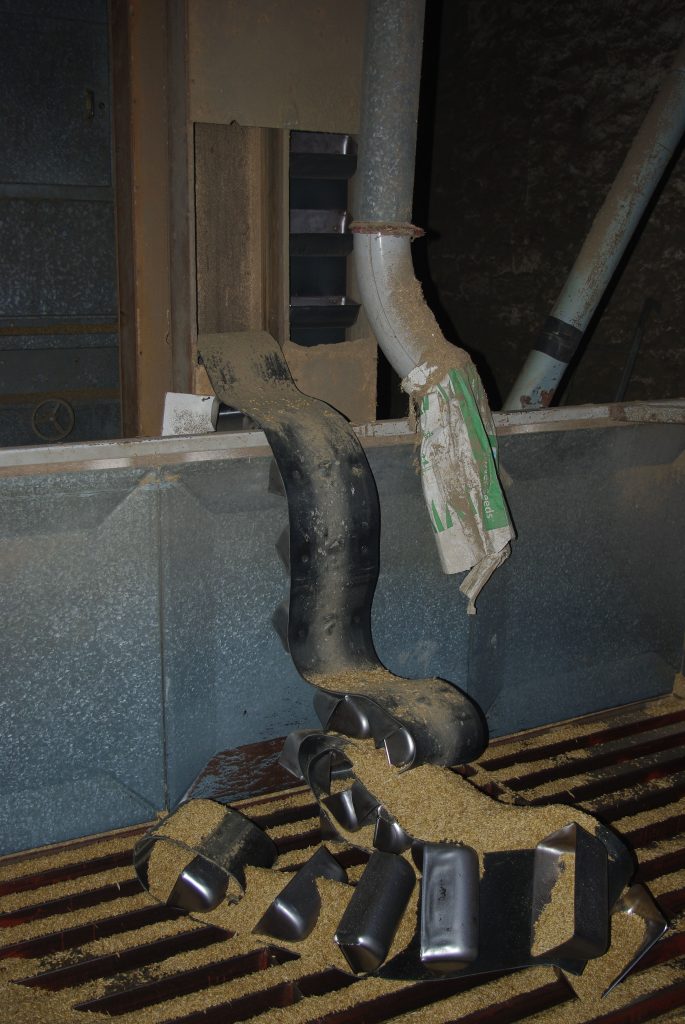
The picture shows the result. The leg on the right is what it should look like. The left leg was the one that took the wet grain from either the pit or the wet bin, and put it in a conveyor which fed the top of the dryer. Thankfully we were able to keep going by drying the grain in batches, rather than continuous flow, and using the one leg to both empty and fill the dryer. It was a slow process, but we only had about 100 tonnes to dry at this point, so we managed.
The Weather
Away back in April I wondered if we were in for a wet harvest, as the spring had been so dry, and so it has turned out. To be fair though, it hasn’t been soaking wet (yet), but there has been some rain most days, which has meant that we never really got a good run at things. The weather station report below illustrates this clearly:
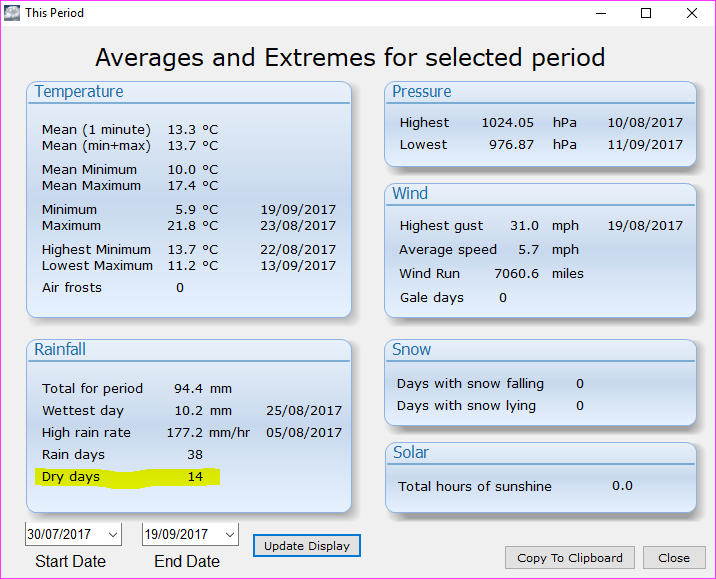
Harvest lasted a total of 52 days, in which only 14 had no rain at all. Yet we had less than 100mm in that time. It is not unknown for a wet month to be in excess of 120mm, so the main problem was the frequency of the rain, rather than the total amount. We were glad we finished when we did, as the good harvest days since the 19th September have been very few indeed.
Harvest Results
Looking at the broad picture it has been an average harvest. The winter barley was disappointing, coming in at 5.74 tonnes/hectare, which is below our 5 year average of 6.66 tonnes/hectare. Partly this was due to the disaster we had in one field that had a bad infestation of sterile brome (1.4 tonnes/hectare). This was our fault rather than the year, and when it is taken out the equation things don’t look quite so poor. Pretty much all the winter barley was up the hill this year, and when compared with similar spring barley, it is holding its own.
Spring barley came in at 6.38 tonnes/hectare, which is slightly above our 5 year average of 6.15 tonnes/hectare. However looking just at the average hides the quite a lot. Yields ranged from 4.02 tonnes/hectare – 7.97 tonnes/hectare, depending on what soil type and where on the farm. Also, all the higher yielding fields were growing either Concerto or Laureate, which went away for malting at a premium.
Partly because of the poor weather we chopped more straw than we normally would. It was hard enough finding good weather to cut the crop, never mind bale the straw, and we still have one field that we sold in the bout still lying there.
In Summary
I think this has been one of the hardest harvests I’ve done, though it may be that my memory is playing tricks. It is never much fun when the farmyard and fields are muddy, and you can’t get on with the work you know needs to be done. As usual I am grateful to the various companies and organisations that helped us. In no particular order: Stuart Miller and the mechanics at Sellars who kept the combine going; Jock Elliot and the drivers at Chrystal Petroleum who somehow managed to keep both the dryer and combine going in fuel even at short notice sometimes, and to Brian and David Addison who were available to help when it was most needed.
I will finish with a picture I took of the combine on the last evening just before I finished. The dogs are perhaps the only ones who are disappointed to see the end of harvest, as they get a far better view from the combine than they do the tractor!
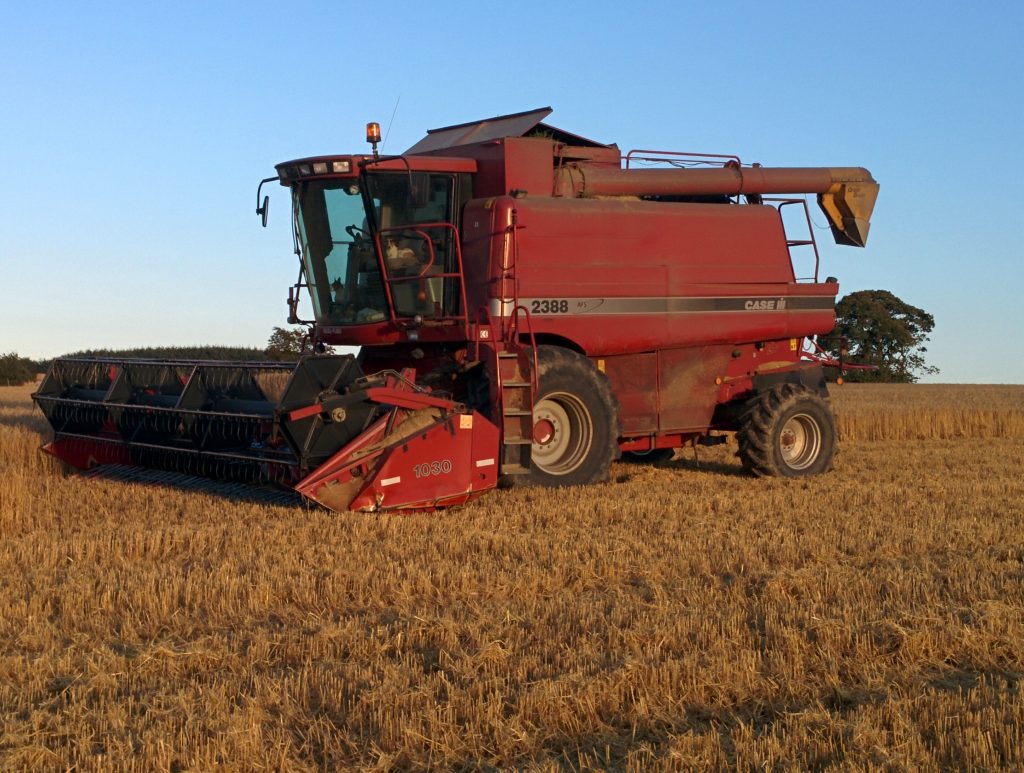